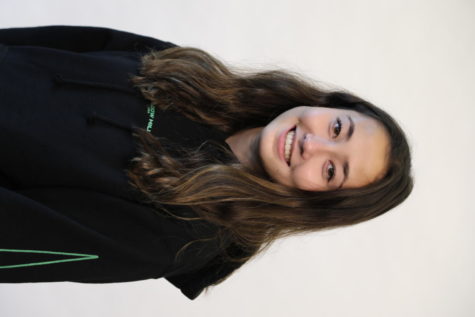
Number of years in The Coat of Arms: 3
Favorite aspect of journalism: writing about topics I'm passionate about, like music.
Interests outside of school: working at Tin Pot Creamery, baking, and dancing.
Class of 2023
May 29, 2023
Kinder most recently completed a sword for his Experimental Archaeology class at Menlo. This is the second sword that Kinder has made. Photo courtesy of Max Kinder
While most residential driveways are used to store vehicles, senior Max Kinder instead uses his to store blacksmithing equipment: his very own anvil and forge.
Kinder first drew interest in blacksmithing towards the start of his sophomore year, during the peak of the COVID-19 pandemic. He thought it the perfect hobby to not only get away from his laptop, but to also spend more time outdoors. While searching online, blacksmithing immediately grabbed Kinder’s attention. He came across several blacksmithing videos on YouTube, and was inspired to order the proper equipment, including an anvil from Amazon. “It seemed really interesting,” he said.
However, according to Kinder, learning how to blacksmith was originally quite difficult; he taught himself by watching tutorials and reading online instruction packets. Kinder experimented by making smaller items, his very first project being a knife. “The knife took a month to make,” he said. At this time, Kinder did not own a real forge yet, either; his first setup instead consisted of a brick oven, charcoal and hair dryer.
With a forge, which functions as a type of hearth for heating metals, the blacksmithing process is easier. Kinder starts by selecting what steel he will use for his creation; steels with higher carbons make better blades, while steels with lower carbons are easier to work with. “I get low carbon steel most of the time,” Kinder said. Kinder also tries to pick steel in a shape closest to what he will be making. Next, he heats the metal with his forge. He uses an anvil, a vice and little tools to bend the metal exactly how he wants. When the object has cooled, he sands it down or adds other decorative touches.
“I also made a bunch of hooks because they are really good practice,” he said. “I use this little [tool], basically like a tuning fork. You put it in a device and it will bend [the metal] for you.”
Since every item Kinder forges is made completely out of melted steel, he must be extremely careful with his equipment. Still, Kinder admits that he often accidentally injures himself. “Basically every time I burn myself,” he said. “Also, blacksmithing is a lot of work, and can be pretty tiring.”
After finishing his sophomore year, Kinder and his family spent the following summer in a small Massachusetts town, where he apprenticed at a local blacksmith shop. Kinder credits this experience to majorly improving his different blacksmith techniques. “I just walked in one day and asked, ‘Can I apprentice?’ And they said, ‘Sure.’”
Kinder started going to the shop two to three times a week, and his tasks varied from day to day. “I would watch what they were doing and help. If they needed me to maintain a fire or hold something while they worked, I would do that,” he said. “If they were not actively doing something or did not need my help, then I would just work in their second forge.”
Kinder’s apprenticeship also included helping run a booth at a week-long county fair. According to Kinder, working at the fair was very different from normal blacksmithing. “At the fair, we usually make things that are pretty quick and look cool while you’re making them,” he said. “So it’s kind of more showy. You get the metal hotter so it glows brighter. We try to be louder with our shapes to draw more attention. That was kind of a weird experience, because [blacksmithing] is usually a very precise thing, and the fair is basically just a lot of messing around.”
Kinder especially appreciates blacksmithing because he has the freedom to create whatever he wants, whenever he wants. “If you spend enough time, you can pretty much make anything,” he said.
Kinder’s various projects also require extremely different amounts of time. “Depending on what you make, the process can be really quick or take forever,” he said. For example, one of Kinder’s favorite projects, a real sword, took nearly 20 hours to finish, whereas fake candy canes only need about 20 minutes.
Kinder is proud of how much he’s grown as a blacksmith since the 2020-21 school year. Although Kinder only spends about an hour a week on blacksmithing currently, he used to work on projects every single day. “I’m most proud of how much my skills have gotten better,” he said. “I can now do projects that used to take me hours in, now, like 20 minutes.” He has now completed between 40 to 50 individual projects, including a portable grill. However, according to Kinder, many of these projects are somewhat identical, for practice purposes.
Currently, Kinder’s blacksmithing equipment lives right in front of his house. “My parents love that I [am a blacksmith,] but they do not love that I take up the whole driveway to do it,” he said. “The anvil’s pretty big, but it’s not insane.” Kinder moves tools that could rust under an awning, but everything else remains on the driveway.
While Kinder has never sold any of his creations before, he would consider doing so this summer. “I would be willing to sell [creations] myself, and I might try this summer,” he said. “But it’s kind of hard to get started with that.” Kinder also plans to maintain blacksmithing as a hobby, even as he moves to college.
Number of years in The Coat of Arms: 3
Favorite aspect of journalism: writing about topics I'm passionate about, like music.
Interests outside of school: working at Tin Pot Creamery, baking, and dancing.
Class of 2023